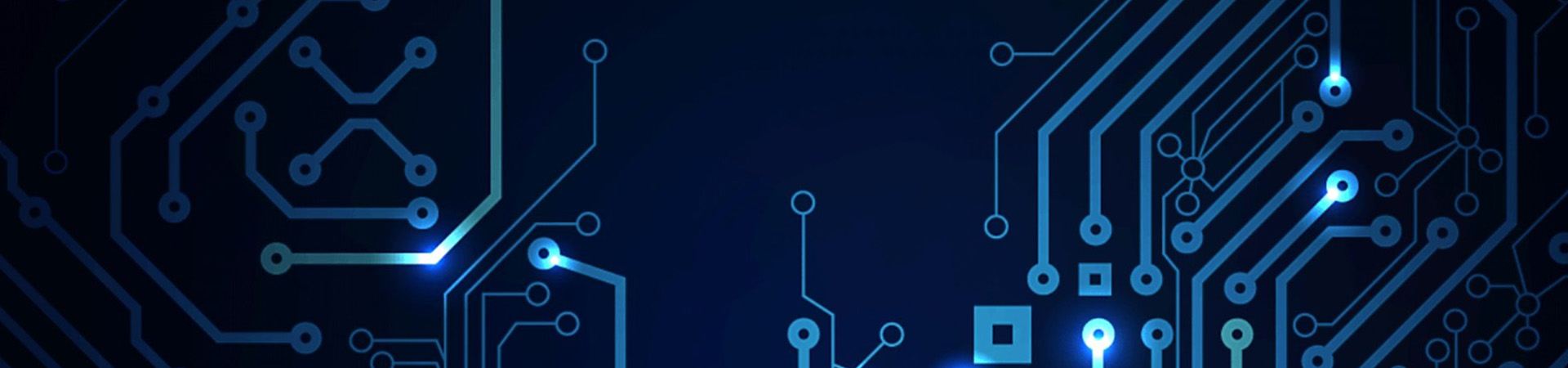
Choosing the Best Surface Finish for Printed Circuit Boards
Most printed circuit boards have a coating, also known as surface finish, on their outermost surfaces. During assembly, the solder paste in the reflow process or solder in the wave soldering process dissolves this coating.
Surface finish on printed circuit boards have two main functions:
- Preventing the copper on the outermost layers from oxidizing and
- Offering a solderable surface
While there are various types of surface finishes for printed circuit boards, some are more popular and versatile than others are. Users are likely to review their considerations for selecting a surface finish from a PCB supplier based on its effect on the circuit board price and its durability. However, depending on the materials the surface finish uses, there can be other considerations like finish compatibility with the termination process in subsequent stages including welding or wire bonding.
The Importance of a Surface Finish
It is necessary to evaluate different surface finishes for knowing the best one for a specific application. After all, solderability of the surface finish contributes the maximum towards problems faced in PCB manufacturing and assembly. It is possible to gauge the importance of selecting a suitable surface finish as the choice can influence:
- The process yield
- The scrap rate
- The ability to test
- The amount of rework
- Field failure rate
- Overall cost of the project
Types of Surface Finishes
Primarily, PCB suppliers offer two types of surface finishes with many sub-types:
Metallic Surface Finishes
- Hot Air Solder Leveling (HASL) — with Lead, or Lead-Free
- Electroless Nickel/Immersion Gold (ENIG)
- Immersion Tin (ImSn)
Attributes of Various Surface Finishes
Hot Air Solder Leveling
During PCB production, the manufacturer holds the board vertically and dips it into a flux bath followed by a dip in a hot vat of molten solder. The molten solder can be the usual tin/lead alloy, or a lead-free solder alloy, depending on whether the board must comply with RoHS directives. After raising the board from the vat, the manufacturer uses hot air knives to level off the surface finish. Although the process produces a homogenous thickness of solder over the entire board, it is not flat enough for dense, high pin-count, close-pitch surface mount components.
Electroless Nickel / Immersion Gold
For ENIG surface finish, printed circuit board manufacturers plate the copper surface on the board with electroless nickel, followed with a thin coating of immersion gold. This effectively shields the copper from oxidation.
Immersion Tin
Manufacturers deposit a thin layer of tin onto the copper surface of the board using a chemical process. Frequently used in high-speed circuits, immersion tin is useful where the manufacturer cannot use nickel or silver. However, presence of tin in proximity to copper allows diffusion between them, resulting in complications.
Selecting the Most Suitable Surface Finish
While different surface finishes have attributes that make it attractive for certain applications, it also implies that the user is making important tradeoffs. The user must consider the impact of the surface finish for all functions, while providing the lowest overall cost. Broad considerations for a suitable surface finish is the one which:
- Offers the largest process window
- Is capable of withstanding multiple reflows
- Offers a reliable and robust end product
- Is easiest for the PCB manufacturer to produce with high yield
- Offers the lowest cost
There may be more technical aspects that need considerations by the OEM, such as:
- Whether lead-free solder is necessary?
- Whether the PCB is susceptible to corrosion, contamination, or breakage from handling?
- Whether forming good wire bond connections is important?
- Does the electronic circuit board use close-pitch components such as BGAs?
- Does the PCB have contacts on its edges?
- Does the PCB require a long shelf-life?
- Can the project absorb the extra cost of adding surface finish?
Comparing Attributes and Functions of Various Surface Finishes
Surface Finish | HASL Lead-Free | ENIG | ImSn |
---|---|---|---|
RoHS Compliance | Yes | Yes | Yes |
Handling Sensitivity | Good | Good | Med |
Fabrication Cost | Low | Med | Med |
Fabrication Cost | Low | Med | Med |
Close-Pitch | Low | Good | Good |
Corrosion Resistance | Poor | Good | Good |
Shelf Life | ~1 Year | > Year | < Year |
Multiple Assembly | Good | Good | Good |
Multiple Rework | Med | Med | Poor |
Solder Wettability | Good | Good | Good |
Co-Planarity | Good | V.Good | V.Good |
Solder Joint Integrity | Good | Good | Good |
High Speed Capability | Poor | Poor | Poor |
Wire Bonding | Poor | Poor | Poor |
Conclusion
Selecting a suitable surface finish based on attributes and functions provides an adequate solution for printed circuit boards in most applications. However, there are several other attributes apart from those listed here, and users must consider many other parameters when selecting surface finish for specific applications.