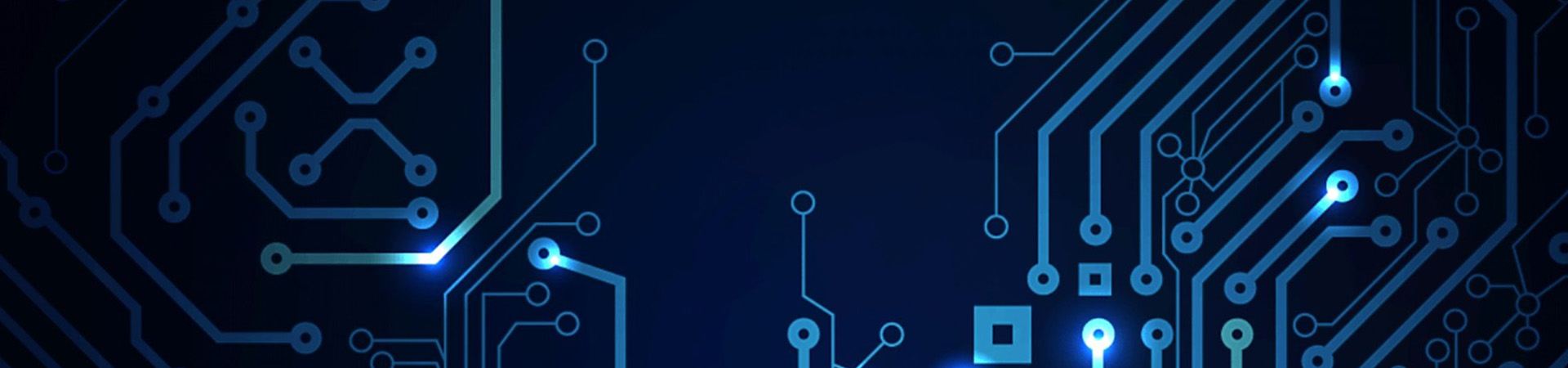
Benefits of Machine Assembly
Assemblers must populate and solder printed circuit boards with components to make them functional. It is essential that they mount the correct component at the right place for the board to function as intended. Depending on the component density and the complexity of the board, there are broadly two ways of PCB manufacturing and assembly—manually and using high precision machines.
Manual Assembly
This type of assembly requiring human hands to populate the board is best when:
- There are only a few components on the board
- The board mainly has through-hole components
- Only a few boards need to be assembled
As the assembly is manual, there is a possibility of errors like wrong components mounted, components mounted at the wrong position, components mounted with the wrong polarity, and missed components.
Moreover, the throughput of manually assembled boards is not very high. Therefore, for situations requiring high throughput, high accuracy and repeatability, high quality, and lower costs, manufacturers prefer using machines to assemble boards.
Machine Assembly
Assembling a printed circuit board with machines requires several steps. It is possible to use manual operations at some steps, but for best results, it is advisable to automate all the steps. Moreover, using surface mount technology vastly improves the efficiency of machine automated assembly. However, the PCB circuit design must be such as to support SMT.
Whether the printed circuit board undergoing assembly is a rigid board, flexible, or High Definition Interconnect type, the major assembly steps are common. These are:
Automated Solder Paste Deposition
Solder paste deposition typically involves the use of a stencil. Stencils are thin stainless-steel sheets with precision cutouts that match pads on the printed circuit board. After proper registration on the board, a squeegee moves solder paste across the stencil, allowing it to drop through the openings onto the pads.
An automated inspection usually follows the solder paste deposition stage to ensure the deposition is clean and without smear. The inspection stage verifies the height of solder paste deposited is adequate to solder the component. If the height is more than the specifications, the volume of the solder paste will be more, leading to solder bridging with the neighboring pad/component. If the height is lower than necessary, it may lead to inadequate or dry soldering.
Advantages of Automated Solder Deposition
The advantage of automation in the solder paste deposition stage is that once the machine is adjusted for the proper deposition height, the results are highly predictable and repetitive, resulting in high throughput. At this point, the automated inspection stage may resort to sampling inspections rather than continuous checking.
Automated Component Mounting
The next stage involves a pick-and-place machine selecting components from feeders and placing them in individual locations on the board. Pick-and-place machines require programming to allow them to operate effectively. These machines generally have many heads that move from the cassettes and reels of components, picking them up and positioning them in pre-programmed locations on the board.
In the initial stages, an automated inspection stage may be necessary to determine a satisfactory outcome of the pick-and-place machine. Once established, the inspection stage may resort to sampling inspections.
Advantages of Automated Components Mounting
After mounting of components, the printed circuit boards travel on conveyor belts through a machine for reflow soldering. The machine typically has a number of sections where the temperature increases following a gradient. At the final section, the temperature is high enough to melt the solder and bond the component to its pad on the PCB. After this, the PCB and its soldered components pass through a gradual cooling section.
For proper reflow soldering, the operator must initially calibrate the temperature profile and the speed of the conveyor for a specific PCB assembly. It is important the printed circuit board and components follow a specific gradient up to the point of actual soldering.
Advantages of Automated Reflow Soldering
Machine soldering is a much faster way of soldering an entire board with several components. Manual soldering typically uses a soldering iron or a hot-air gun to melt the solder. This has the disadvantage of causing a possible dislocation of the component, as most SMCs are very tiny. Moreover, the soldering iron bit has a finite size that is many times the pitch of high-density components, leading to solder shorts.
Apart from increasing the throughput PCB manufacturing and assembly tremendously, machine soldering also reduces the possibility of errors like solder shorts, missed solder joints, dry solders, burnt components, and many more that a manual soldering process inevitably causes. Compared to the uneven soldering from the manual process, automated soldering offers an even and uniform soldering for all the components in one go.
Automated Testing
Automated testing may use one of two methods—a fixture or flying probes. For both, it is necessary that the PCB circuit designer has provided test pads at strategic points on the board during its design.
Advantages of Automated Testing
Using a dedicated fixture with multiple probes drastically reduces the testing time for boards. A fixture usually tests multiple parameters at a time with high accuracy, which would be impossible in a manual operation. However, fabricating a specific fixture for an individual board assembly is an expensive process, and manufacturers prefer using fixtures only when the production run is of a substantially large quantity.
The other method of automated testing during PCB manufacturing and assembly uses a pair of flying probes or more. The testing machine is programmable, and the test probes connect to various test pads serially to check and measure parameters. Although the speed of testing is lower than that using a fixture, the advantage is lower cost, repeated use, and rapid reconfigurability when producing many types of boards in quick succession.
Conclusion
One of the major advantages of machine assembly of printed circuit boards is overcoming human error. There are several reasons humans are error-prone. One of them is variable judgment and the other is operational fatigue. Human judgment is highly subjective, and dependent on the individual, leading to different conclusions by separate operators. Operational fatigue sets in for human operators after a few hours of intense concentration, leading to operational errors. Machines are devoid of both these shortcomings—their judgment depends on a few rules programmed into their memory, and machines do not experience fatigue, provided they undergo regular preventive maintenance. Using machine assembly also has the benefits of reducing overall manufacturing costs.