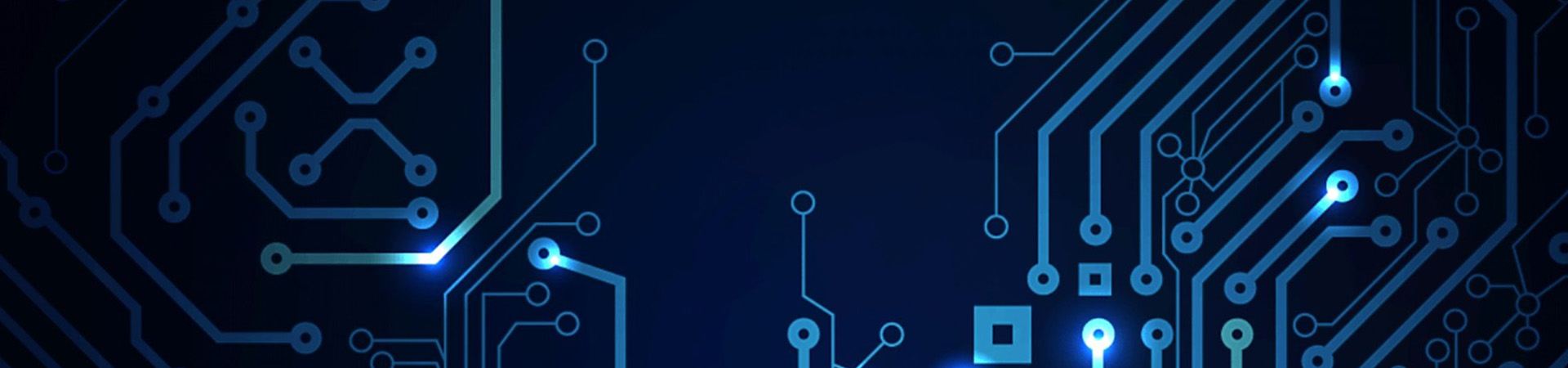
Comparison Between Through Hole Assembly & SurfaceMount Assembly
Electronic products typically use two types of printed circuit boards. One uses through hole assembly, and the other uses surface mount assembly. PCB circuit design and the assembly techniques for the two differ.
The electronic component industry has two basic types of products—they offer electronic components that have long leads and others with very short leads. The first type, those with long leads, are known as Through Hole Components or THCs, and those with short leads are Surface Mount Components or SMCs. The difference in the structure of these two types of components results in different requirements in assembly and soldering techniques.
Through Hole Components
Through hole components dominated the electronic manufacturing industry much before the surface mount components appeared. Assembling THCs requires threading their leads through holes in the printed circuit boards before anchoring them by soldering.
Through Hole Assembly
It is possible to have two types of assemblies for THCs:
Manual Through Hole Assembly
Earlier, manual assembly was the main mounting method for THCs. Operators must manually bend the leads to fit the pitch of the component on the PCB before inserting them. Depending on the hole pitch, they can mount the components axially or radially. In axial mounting, the axis of the component will finally lie parallel to the board surface. In radial mounting, the axis of the component will remain perpendicular to the surface of the board.
Automated Through Hole Assembly
Automated methods of mounting THCs allow faster assembly. This is usually done in two stages. In the first stage, the operator mounts components with two and three leads. They mount ICs later. For the first stage, they prepare a mounting scheme for the components on the PCB, and feed this sequence into a computer. The computer controls a sequencing machine that picks up the components from their reels and creates a new reel that matches the programmed sequence. The programmed sequence also has information on the coordinates of each component, pitch, and orientation.
The operator mounts this new reel into the automated insertion machine. The machine inserts each component in its designated position, after cutting and picking it from the reel and bending the leads to match its pitch. Before insertion, the machine checks for the proper orientation and cuts off the extra leads. After inserting the component, the machine clinches or bends the leads so that the component does not fall off the board.
To facilitate proper soldering, the PCB circuit design must incorporate a teardrop on each pad. For all THCs with two leads, the teardrops on the pads face each other, as the machine will clinch the leads inwards. For THCs with three leads, the outermost teardrops point away from each other, as the machine will clinch the two outer leads away from each other.
The automated insertion machine mounts the ICs next. Most through hole ICs have dual-in-line packages. After placing the IC in its position, the machine clinches two pins diagonally opposite each other to prevent the IC from falling out of the board.
Wave Soldering Through Hole Components
Once the machine has mounted all the THC components, the assembly then proceeds for wave soldering to anchor the components on the printed circuit board. Wave soldering machines have a tub of molten solder with a pump inside. The pump pushes molten solder upwards through a chute. A conveyor carries the pre-heated PCB assembly over the flowing molten solder such that the solder touches the board on its lower surface. This causes the molten solder to attach itself to the pads and component leads. As the board passes over, the solder cools and solidifies, anchoring the component leads to the PCB pads.
For proper soldering, the operator must adjust the speed of the board through the wave soldering machine, the pre-heat temperature, the height of the solder wave touching the board, and the temperature of the molten solder.
Surface Mount Assembly
Unless the PCB uses only a few large SMCs, the industry prefers automated assembly to manual assembly.
Automated Surface Mount Assembly
Manufacturers create SMC passive components in very small packages, with end caps acting as the leads. Active SMC components vary in structure, with small pins, either jutting out or folded inwards to act as connecting leads.
SMCs do not require holes for mounting them on the printed circuit board. Anchoring them on the board requires placing them on designated PCB pads and soldering them in place.
Solder Paste Application for SMCs
In contrast to THC assembly, soldering SMCs is rather awkward after mounting them. The proper technique is to apply a small amount of solder paste on the pads before placing the component. For accuracy, the operator uses a stencil that has holes cut into it matching the position of individual components. A squeegee forces the solder paste through these openings, depositing the appropriate amount on the PCB below the stencil. Once the solder paste application is complete, the board can proceed with the placement of components.
Pick-and-Place Technique of Mounting SMCs
As most SMCs are physically small, manually placing them is not an efficient option. Rather, pick-and-place machines can do the job with high precision and efficiency. The operator must program the computerized pick-and-place machines with the proper coordinates of the components on the board, their orientation, and polarity.
After programming the machine, the operator loads into it all the reels, cassettes, or trays of the different SMCs that the machine must use. The pick-n-place machine may have multiple heads for pneumatically picking up individual SMCs from their reels and placing them on the solder paste on the board, according to the program.
Reflow Soldering of Surface Mount Components
On a board mounted with SMCs, all components are on the top surface. Therefore, it is not possible to use the wave soldering machine. Rather, the operator solders the assembly with a reflow soldering machine. A conveyor transfers the board mounted with the SMCs through the reflow machine. Inside, there are several pre-heat zones that slowly raise the temperature of the board assembly before it finally reaches the soldering zone.
In the soldering zone, the temperature is such as to melt the solder paste, making it flow, allowing it to bond to the PCB pad and the component lead. Once the PCB assembly passes this zone, the temperature drops to allow the board assembly to cool. The molten solder then solidifies and anchors the components on the board.
To obtain a reliable solder joint, the operator must control the speed of the conveyor carrying the board and components through the reflow machine, the temperature of the various pre-heat zones, and the temperature of the soldering zone.
Comparison Between Through Hole Assembly and Surface Mount Assembly
- Through hole assembly offers a stronger mechanical bonding. Therefore, this technology is applicable for products that must undergo high mechanical stress.
- The larger size of THCs does not allow achieving very high PCB density.
- Through hole assembly offers easy manual adjustments and component replacement.
- Prototype circuit boards and testing is easy for boards with through hole assembly.
- As THCs must be threaded through holes in the PCB, assembly time is higher.
- Manual soldering or wave soldering of THCs can result in issues with reliability, repeatability, and reduced manufacturing efficiency.
- As surface mount assembly does not use holes, the board cost is lower, and reliability is higher.
- Pick-and-place machines can reach very high efficiencies and high throughput.
- The Reflow technique of soldering surface mount assemblies results in high reliability solder joints, with high repeatability.
- Surface mount assemblies are more susceptible to mechanical stress in comparison to through hole assemblies.
Conclusion
Although surface mount assemblies are more efficient, cost-effective, and smaller than their through hole assembly counterparts, the industry uses through hole assemblies for printed circuit boards where the product must face considerable mechanical and thermal stress. The PCB circuit design and printed circuit board fabrication for the two differ accordingly.