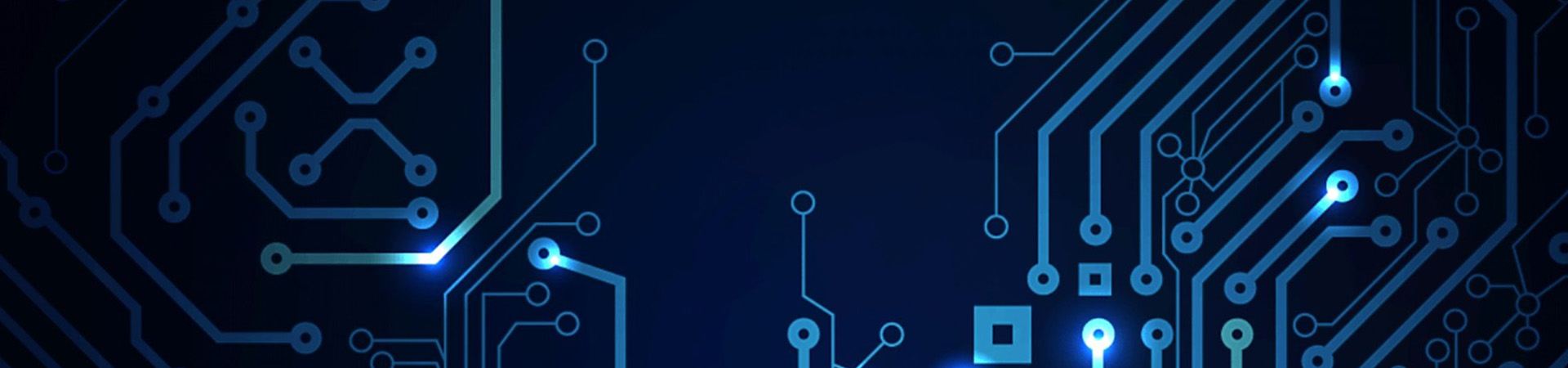
DFM Guidelines for Solder Mask Design
Precision and reliability are important in modern PCB design. One of the design aspects that has a huge impact on performance and manufacturability is solder mask design. The solder mask is a thin polymer layer deposited on the copper traces in PCB fabrication. As designs are more compact and components are densely packed, one has to learn and follow the DFM guidelines.
DFM for solder mask design ensures electrical soundness in layout efficiency, and defect-free manufacturing. This blog discusses the key DFM guidelines for solder mask design. We will know the best practices and standards that aim to bridge the gap between design intent and manufacturing capability.
Purpose of DFM (Design for Manufacturability)
The goal of DFM is to create a smooth interface for design and manufacturing through collaboration from the beginning of product development. In the past, due to miscommunication among the designers and manufacturers, there had always been delays in production, costly changes, and product defects. Involving DFM ensures all functions communicate across the board, enabling engineers and manufacturers to discover and fix design problems early in the process. This essentially allows better time management and cost control, leading to a faster and smoother production process.
Essential DFM Guidelines for Solder Mask Design
For reliable PCB fabrication and smooth manufacturing, the solder-mask design has to comply with essential DFM guidelines.
1. Adequate Mask Coverage and Clearance
The solder mask should expand slightly beyond the copper pads for proper alignment. It is necessary to have sufficient isolation between copper pads and component pads to via holes to prevent solder bridging. The clearance of 0.1 to 0.15 mm between traces and edges of the solder mask must be provided so that there are no insulation problems.
2. Select the Right Solder Mask Type
NSMD (Non-Solder Mask Defined) pads are used for fine-pitch components as they have higher solder joint reliability. In comparison, Solder Mask Defined SMD pads are used to relieve stress from certain solder joints. For vias, tenting with a solder mask can prevent solder wicking and protect the board.
3. Improve Application and Thickness of Solder Mask
A thickness of 0.01 mm to 0.03 mm can provide good protection. LPI (Liquid Photoimageable) solder mask application is most suited for complex designs where the solder masking is done precisely. On the other hand, dry film suits less complicated boards that require uniform coverage.
4. Define Mask Relief Areas and Bridges
Solder masks must be removed from regions like heat sinks for thermal purposes. Pad-to-pad webs should be a minimum of 4 mils wide to avoid solder bridging, especially for common green or red mask masks.
5. Validate Design with Manufacturer Capabilities
Always confirm the tolerances and capabilities of the solder mask with your PCB manufacturer. Then generate clear Gerber files with the actual solder mask layer, creating proper production without delays.
Conclusion
The effective design of solder masks ensures reliable PCB fabrication by avoiding solder bridging, oxidation, and possible electrical shorts. Other design parameters are the expansion of the pad-to-mask area, proper selection of via tenting methods, and the ability for thermal and mechanical performance. Correct solder mask layer thickness and application methods will further increase manufacturing capability.
At PCB Power, we bring together cutting-edge design insight and manufacturing precision. From accurate solder mask application to comprehensive DFM checks, we ensure that your PCBs are production-ready, high-performing, and reliable — every time.
Get in touch to get an instant quote today.
FAQs
1. Why is solder mask expansion critical in PCB design?
Solder mask expansion compensates for set-up errors during manufacture, thus preventing exposed copper and possible shorts.
2. What is the difference between NSMD pads and SMD pad designs?
NSMD pads have solder mask openings that are larger than the copper pad, allowing the entire pad to be exposed for soldering. This improves solderability and inspection. SMD pads, on the other hand, have mask openings smaller than the copper pad, overlapping the pad edges for added mechanical strength.
3. What is the role of via tenting in the reliability of PCBs?
Tented vias have a solder mask over the annular ring, preventing solder wick during assembly and also reducing the risk of oxidation.
4. What thickness of solder mask is suitable for high-density designs?
A choice of an ideal thickness would be 0.01 to 0.02 mm for fine-pitch components. Therefore, insulation and precision are balanced.
5. How can I avoid solder mask bridging between pads?
Maintain at least a 4 mil solder mask web between pads and avoid sharp angles around the pads to reduce stress fractures.