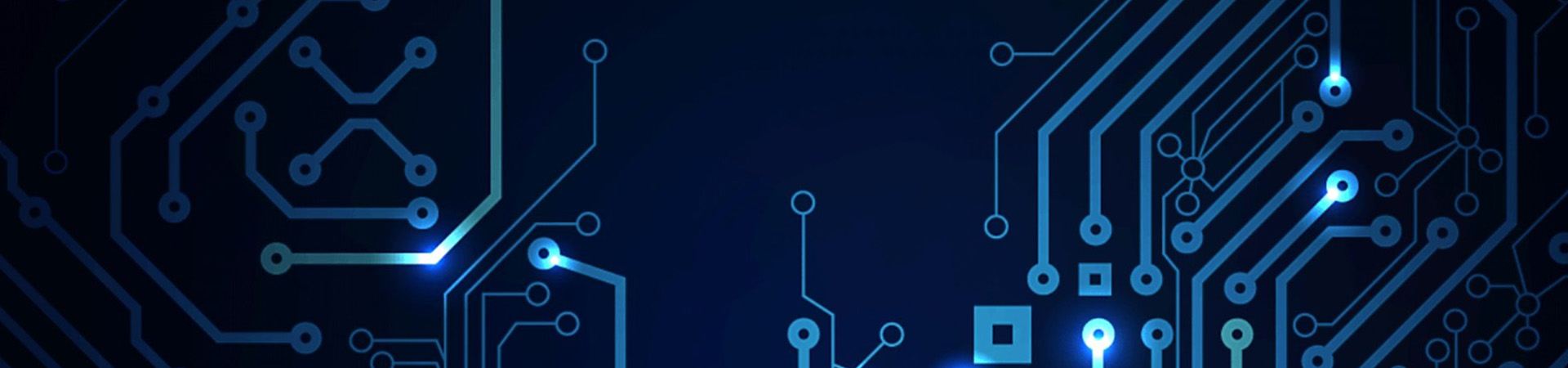
How are Flexible Circuits Made?
Flexible circuit board fabrication starts once the PCB design receives a final approval and the manufacturer receives the final manufacturing files. The fabrication process is similar to that of regular rigid printed circuit boards. The process proceeds in two steps—one for the inner layers, and the other for the outer layers for multilayered boards. Each consists of executing several sub-steps before the final coverlay application.
Structure of Flexible Circuits
Most flexible printed circuit boards are actually part of a rigid-flex system. This consists of numerous rigid boards interconnected with flexible circuits. Flexible PCBs can eliminate the need (and cost) of connectors and cables, improve connection reliability, and reduce assembly time. They also reduce assembly costs and overall device dimensions. Flexible printed circuits boards are compatible with virtually any type of connector or component and work well with ZIP connectors. Simply, a flexible PCB board does not contain as many potential sources for failure, and this enhances their reliability.
Manufacturing Process of Flexible Circuits
Manufacturing the rigid-flex electronic circuit board involves several steps like:
Base Preparation
The fabricator prepares the laminates for the stack-up. These are typically copper clad laminates. The copper layers may have an anti-tarnish coating, and the fabricator must remove it by chemical means. If the boards are small, the fabricator starts with a panel in which he arranges several individual boards in the form of an array.
Imaging the Design
The fabricator generates films of the circuit patterns from the Gerber files through a process of photo imaging or screen printing. Each film for the outer layers has a black portion representing the copper traces, pads, and circuits on the PCB design. The clear areas on the film represent the non-conductive areas of the circuit. Films for the inner layers are the opposite. Here, clear areas of the film represent the copper patterns, while the black, opaque portion represents the non-conducting areas of the circuit.
The fabricator also adds registration holes in each film. These will assist the fabricator when aligning the films during later stages of the manufacturing process. The films need safe storage to avoid attracting dust and scratches.
Printing Inner Layers on Copper
The fabricator starts with a copper clad substrate layer. The most commonly used material for the substrate is polyimide (PI), characterized by its high resistance to traction and temperature. The steps involved in this process are:
- Covering the copper layers with a photo-sensitive resist film
- Placing the film of the layer on to the photo-sensitive film
- Exposing the film and photo-sensitive film combination to UV light. The UV light passing through the transparent parts of the film hardens the photo-resist, while the photo-resist under the black parts of the film remains unhardened, as the UV light cannot penetrate the black opaque parts.
Etching Unwanted Copper
The fabricator exposes the copper clad substrate to etching chemicals. The chemicals remove the unwanted copper from the unhardened areas, while the hardened photo-sensitive film prevents removal of copper under it.
After the etching is completed, the fabricator washes the substrate with alkaline solutions to remove the leftover photo-resist film. The substrate undergoes an examination to detect the presence of any errors. Now the substrate retains only the copper features, traces, and pads that the layer will use.
The fabricator creates all the layers necessary and cleans them thoroughly to remove all traces of chemicals.
Automated Optical Inspection (AOI)
The fabricator subjects each layer to a rigorous stage of inspection involving automated methods. The AOI system scans each layer with a laser, recording the surface of the layer. The system then compares each scan with a reference and flags any defects.
After a successful inspection, the layers are ready for lamination and bonding.
Lamination
The fabricator now sandwiches the outer layers and the inner layers. For this, the fabricator must align each layer using the registration layers present in each substrate layer. The fabricator separates each layer with a B-staged modified acrylic adhesive for electrical insulation. Once the stack is complete, the fabricator places metal press plates on both sides of the stack, making sure the stack fits perfectly without being able to shift.
Fusing and Bonding
The fabricator places the stack in a mechanical press and applies pressure to fuse the layers. A computer controls the amount of pressure applied, and also controls the amount of applied heat. The heat and pressure serves to fuse and bond the various layers in the stack into a complete electronic circuit board.
Drilling
The fabricator then drills the through holes and vias in each layer, depending on the drilling information provided in the Gerber file for that layer. This may involve mechanical drills or lasers as necessary. Drilling is the most critical step in the flexible circuit board fabrication.
Plating the Holes
The fabricator electroplates or chemically plates the substrates to fill up the drilled holes with copper. This allows one layer to connect to another layer through vias and through holes.
Printing and Etching Outer layers
The process is the same as applicable for the inner layers.
Coverlay Application
The fabricator applies a coating of coverlay to protect the PCB from harsh environments. The coverlay consists of a solid sheet of polyimide with a layer of flexible adhesive. The fabricator laminates this under heat and pressure to adhere to the circuit surfaces. Drilling, routing, or laser cutting methods are necessary to create the required component feature openings on the surface.
Stiffener Application
Among the two most common stiffener materials that fabricators use are FR-4 and Polyimide. They use FR-4 stiffener to provide support to areas of a flex design that have components and or connectors attached. They use Polyimide stiffeners commonly in designs that connect to a ZIF (Zero Insertion Force) connector.
Attaching Stiffeners
Fabricators attach stiffeners using either a thermally bonding adhesive and laminating it under heat and pressure, or a PSA (double sided tape) and placing it manually. Although the preferred method is thermal bonding with adhesive, design limitations may require the use of a PSA. Thermal adhesives are the same flexible epoxy or acrylic adhesives that fabricators use to attach coverlays to the flex circuit and result in a permanent bond.
Conclusion
For flexible circuit board fabrication, designers and fabricators must select the optimum materials. They must also balance available options while factoring in the cost of materials and performance requirements.