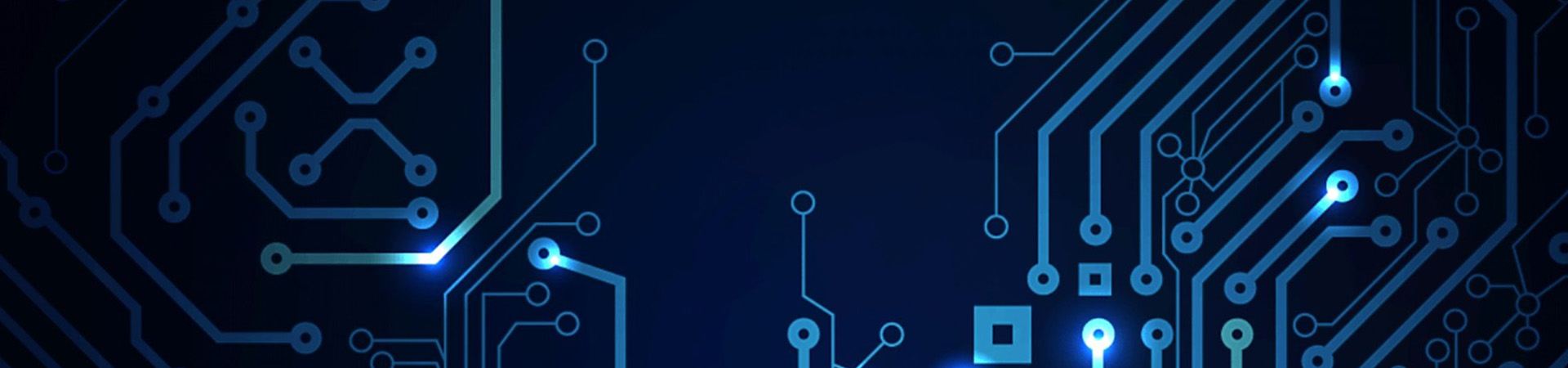
Importance of PCB Thickness and Power Handling
The thickness of a Printed Circuit Board is the sum of the thickness of different layers making up the board. Major contributors to the PCB thickness are the core layer, prepreg layers, and copper layers, with the solder mask and silkscreen layers contributing to a much lesser degree. Of these, the thickness of the core layer contributes to the rigidity of the board, the thickness of the prepreg layers contribute to the insulation, and the thickness of the copper layers contribute to the conductivity and resistance. PCB thickness, therefore, plays a significant role in its functionality.
Constituents of PCB Thickness
PCB Core
The core of the PCB, also known as the substrate or dielectric is the insulating material separating two copper layers. In a double or multi-layered board, a copper-clad constitutes the core, and provides the main thickness to the stack-up. During the fabrication process, the thickness of the core does not change.
Internal Layers
These are additional dielectric supporting the multiple copper layers on either side of the core. Manufacturers adjust the thickness of these layers to achieve a certain configuration of thicknesses.
Copper Layers
The number of copper layers and their weight adds to the overall PCB thickness. Any plating on the copper layers adds to this thickness.
Prepreg Layers
Some PCBs also carry two or three prepreg layers between two cores. Although this adds to the stiffness of the PCB, it also increases the thickness.
Importance of PCB Thickness
Industrial users of PCBs prefer them in standard thicknesses that not only simplifies design, but is also effective for manufacturing equipment and in optimizing costs. The PCB industry provides boards of thickness 0.3-0.8 mm in increments of 0,1 mm, and 1.0, 1.2, 1.6, 2.0, 2.4, and 3.3 mm thereafter. In imperial terms the standard PCB thicknesses are 0.0079 inches, 0.020 inches, 0.016 inches, 0.093 inches, and 0.125 inches. However, PCB designers often design their boards with non-standard thicknesses also to meet operational requirements.
Designers define the thickness of their PCBs depending on its application. Major considerations for deciding on the PCB thickness depends on:
- Flexibility
- Current Carrying Capability
- Materials used
- Number of Layers
- Signal Integrity
- Vias used
- Operational Environment
- Manufacturing Machinery
Flexibility
Applications that require lightweight PCBs can afford to have thin boards. Boards that carry heavy components must be thicker to prevent breakage.
Current Carrying Capability
Since copper layers carry all the current, copper weight plays a significant role. Standard copper weight is 35-70 microns (1 to 2 oz), and manufacturers adjust this thickness according to the board requirements. Boards that must carry higher current need copper weight to be higher, and this increases the overall PCB thickness.
Materials Used
The core and prepreg that the manufacturer uses for the PCB also contribute to its overall thickness. These also provide the board with its stiffness and structure. Therefore, the choice of the material for both the core and prepreg are an important issue for the longevity of the board. Both laminates and substrates making up the core and prepreg are available in various options. Designers can therefore, select suitable materials for deciding the thermal, mechanical, and electrical properties of the board, while at the same time determining the overall thickness of the board.
Number of Layers
The board thickness also depends on the number of layers in the PCB. However, if the designer has constrained the manufacturer to keep the thickness to a specific value, they may have to adjust the thickness of individual layers to achieve it. However, this becomes more and more difficult for the manufacturer as the number of layers in the board goes up.
Signal Integrity
If the board carries high-speed signals, the designer may have to place several traces with defined impedance characteristics. This requires layers with a defined geometry and hence, may impact the overall thickness of the board.
Vias Used
Printed circuit boards use different types of vias like blind vias, buried vias, and through vias. The diameter of the vias influences the thickness of the board. If the board must be thin, the via diameters must be small. Therefore, for very thin boards, micro vias are the right choice, as a laser beam drills them, and hence, they have very small diameters.
Operating Environment
A thin PCB may not be suitable for a rugged operating environment where it is subject to vibration. Such applications require a thick PCB to avoid damage. Therefore, the designer must also consider the operating environment before deciding on the thickness of a PCB.
Manufacturing Machinery
During circuit board fabrication, the machinery must be capable of handling the board thickness adequately. This is important while drilling the PCB and depanelizing individual boards from a panel. The drilling machine must be capable of drilling through holes of the required diameter. Depanelization requires scoring for thick PCBs, and routing for thinner ones.
Power Handling and PCB Thickness
As explained above, higher the power handling capability of the PCB, greater is its thickness. As copper traces in a layer carry the current, their cross-sectional area must be adequate to present a lower resistance when handling the enhanced current flow. Lower track resistance is important as it keeps the temperature of the board within limits. To increase the cross-sectional area of a copper trace, the designer has three choices—making the copper trace wider, adding more layers, or making the copper trace thicker.
Wider Copper Trace
If the designer has ample space on the board to increase the width of the trace, they can continue using the standard copper weight of 35-70 microns (1 to 2 oz). By increasing the width of the copper trace, the designer effectively increases its cross-sectional area, reducing its resistance to the increased current flow.
If the size of the board restricts the designer from increasing the width of the trace to the desired extent, the designer can take recourse to increasing the number of layers or increasing the copper weight.
Higher Number of Layers
By increasing the number of layers, the designer can use multiple traces on adjacent layers to share the current flow. Although the designer continues to use the standard copper weight of 35-70 microns (1 to 2 oz), they effectively increase the cross-sectional area by using multiple traces in parallel. However, additional layers contribute to higher overall PCB thickness.
Higher Copper Weight
If the above two solutions are not viable, the designer can opt for using a layer with higher copper weight. Using a thicker copper layer allows the designer to increase the cross-sectional area of the trace, but without increasing its width. However, a board with a higher copper weight increases manufacturing complexities, apart from making the board thicker overall.
Thermal Considerations
All copper traces have their own internal resistance that opposes the flow of current, raising the temperature of the track in the process. The designer must reduce the resistance of the track to the extent that the increase in temperature remains within limits.
Current passing through the track causes it to heat up, and it loses heat through convection to the surrounding air, thereby stabilizing the temperature. However, this is true only for the traces present on the outermost layers of a multi-layered board.
For traces in the inner layers, heat removal is only through the PCB material, which is less effective than air. Designers must compensate for this difference when designating traces carrying high currents in inner layers. The alternative is to assign high current traces to only the outermost layers.
Deciding PCB Thickness during Design
One of the factors that influences PCB thickness at the start of the design process is the cost of the board. This prompts most designers to start with a standard thickness, and making the necessary change as the design progresses. While making these changes, the designer must keep their focus on certain issues like:
Manufacturing Capabilities
In case the PCB thickness works out to be non-standard, it may be necessary to evaluate manufacturers early on who can fabricate boards with that thickness. However, manufacturing non-standard products generally results in higher costs.
Turnaround Time
Manufacturers can fabricate boards with standard thicknesses while making little or no changes to their manufacturing processes. However, if the board has a non-standard thickness, they may require a change in processes and equipment settings for accommodating the special requirements of the design. This can affect the turnaround time, and the designer must factor this in their schedule, after a discussion with the manufacturer.
Additional Expenses
The designer must also evaluate whether the extra expense of their non-standard board will be conducive to their business. As compared to boards with a standard thickness, a board with a non-standard thickness will not only be more expensive, but may also arrive after a delay. A board with a standard thickness but made of special materials, may be more expensive than a regular PCB, but may not involve a delay in fabrication. Designers may explore such options for a trade-off, rather than opting for a custom-thickness board.
Conclusion
There is an intimate relationship between PCB thickness and its power handling capacity. PCBs meant to carry higher power, whether higher voltage or higher current, are usually thicker. Higher amounts of insulation, lower track resistance, and higher mechanical sturdiness are the typical reasons for the increase in board thickness.