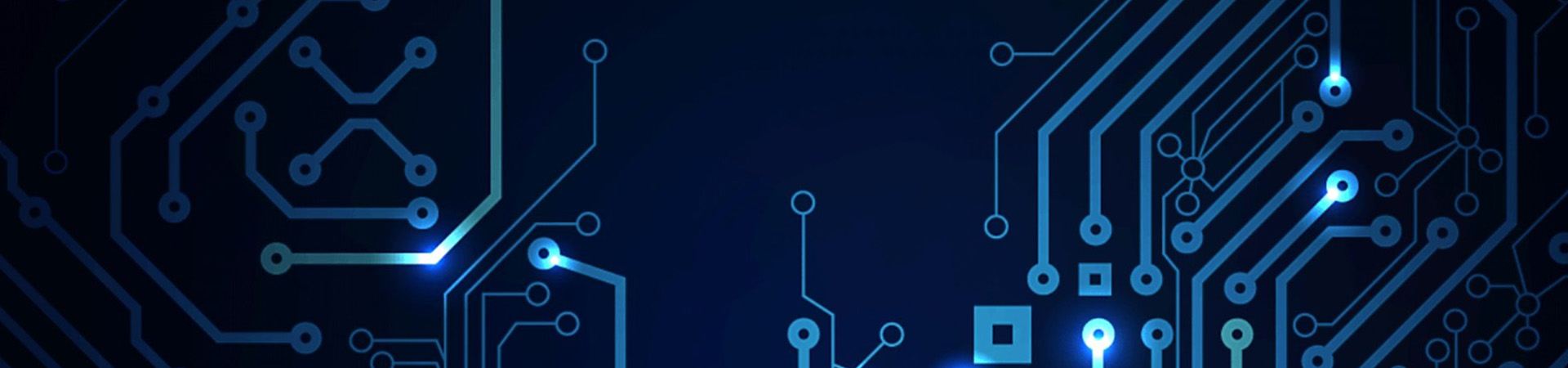
Panelization is a technique where individual PCB units, initially manufactured as separate entities, are interconnected to form a cohesive array, functioning as a singular processing piece for the PCB assembler. This approach proves particularly advantageous in various scenarios.
Firstly, for high-volume production, a well-designed panel can significantly economize both time and costs. By consolidating multiple small-sized PCB units into a single array, the manufacturing process becomes more streamlined and efficient.
Secondly, panelization contributes to the safety of the end product. The interconnected nature of the panel resists the vibrations and shocks typically encountered during the assembly process. This added stability ensures the integrity of the individual PCB units, promoting the overall durability of the final product.
Thirdly, the technique enhances speed and efficiency in production. Processing a multitude of boards simultaneously as part of a single, larger array proves to be more time-effective than handling each unit separately. This approach not only accelerates the production timeline but also meets the minimum size requirements, making it more manageable as a single, unified piece.
Furthermore, panelized PCBs become essential in certain cases of automated assembly. To facilitate the seamless movement of PCBs along conveyors from one machine to another during automated assembly, a tooling margin is necessary. The interconnected nature of panelized PCBs accommodates this requirement, ensuring smooth transitions and accurate automated assembly processes.
PCB Panelization Methods
Understanding these options is key to tailoring PCB fabrication designs for optimal performance in various electronic devices.
V-Score Panelization
This widely used method employs V-shaped grooves to separate individual PCBs, removing around a third of the board's thickness from the top and bottom. The remaining section between the grooves proves to be surprisingly strong. Machine-based breakout processes are preferred to avoid potential stress on the PCB and its components during manual breaking.
Tab Routing Panelization
In scenarios where V-grooves aren't suitable, tab routing comes into play. PCBs are pre-cut from the array and held in place with perforated tabs. This method, which accommodates designs with edge-hanging components, stands out for its versatility. Notably, it allows for manual breaking without the need for specialized tools.
Solid Tab Panelization
This involves designing arrays with solid tabs between each board to enhance overall strength. However, the depaneling process for this type of PCB panel necessitates the use of either a depaneling router, a laser-cutting machine, or a hook-shaped blade tool. Deploying a router may generate dust and vibrations, while a laser cutter proves to be exceptionally costly and ineffective for boards exceeding 1mm in thickness. The hook-bladed alternative, though more budget-friendly, is inefficient and susceptible to blade rotation. Consequently, this method is less prevalent compared to the other two alternatives.
Instructions for Breaking Out PCB Boards
Selecting the appropriate method for breaking out the PCB boards depends on factors such as the type of panelization, the scale of production, and the desired level of precision in the breakout process.
Breaking Tabs by Hand
- Manually bend perforated tabs to break individual PCBs from the panel.
- It is simple but requires precision to avoid damaging the PCB or it’s components.
- Suitable for tab-routed PCBs, offering a hands-on approach.
Breaking Tabs by Machine
- Use a machine for controlled and efficient tab breaking.
- It is ideal for larger-scale production, ensuring clean and accurate separation without risking PCB damage.
- Provides speed and consistency.
Breaking V-Grooves by Hand
- Manually separating V-groove-scored PCBs is not recommended due to the risk of uneven breaks and potential board damage.
- Hand breaking can stress the PCB and its components.
Cutting V-Grooves
- Machine-based process using an angled blade creates V-shaped grooves between PCBs on a panel during manufacturing.
- It enhances precision and consistency, reducing the need for manual breakout.
- Commonly used in PCB panelization for high precision.
Efficient PCB fabrication array designs significantly impact component success and project costs. The key to the design is to choose the right PCB panelization services.
We are a seasoned EMS manufacturer with over 25+ years of experience. Our commitment extends beyond timely deliveries; we provide high-quality engineering services with every project.