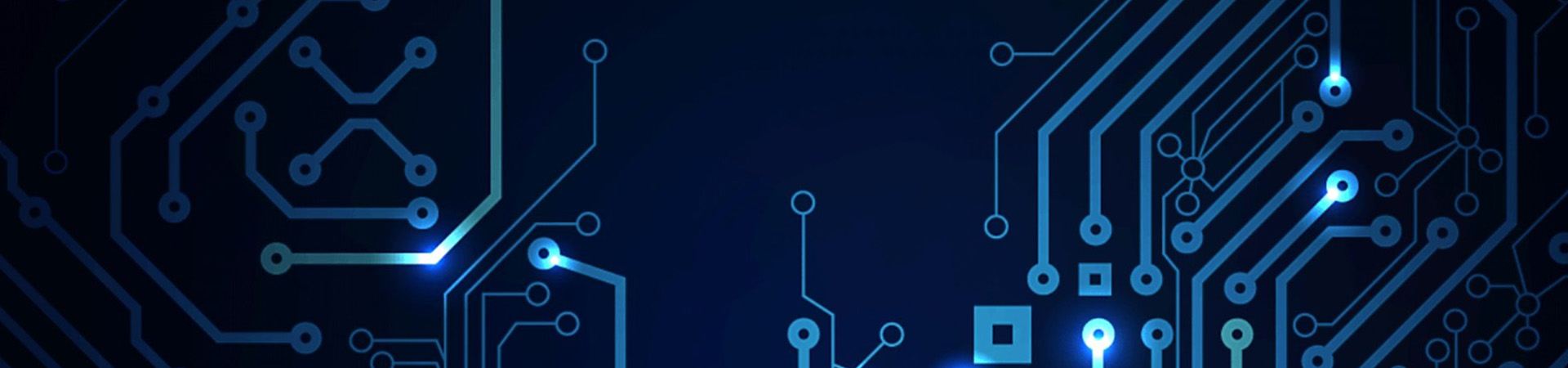
Printed Circuit Boards play a vital role, powering our devices. Among the crucial stages in PCB fabrication is drilling. In this blog, we'll explore the importance, mechanics, tools, and machines involved in PCB drilling, revealing the intricate process of transforming a plain board into a functional circuit.
The process of creating holes in a PCB board is known as PCB drilling. This is essential to making your carefully planned PCB layout work. Even though it sounds like a simple concept, making holes that are accurate and of good quality requires knowing the process inside and out and what factors affect PCB board fabrication.
Role of Drill Holes in PCB Board Fabrication
A printed circuit board has vias-plated through-holes, buried vias, blind vias, and microvias—that link various conductive layers and provide the circuit's electrical pathways.
Component holes:
These provide a space for electronics components such as capacitors, resistors, and ICs to be soldered onto the board.
Mechanical holes:
These allow you to attach the printed circuit board (PCB) to other parts or housings, which gives it structure.
Drilling holes precisely and to a high standard is crucial to the functionality, reliability, and performance of your finished printed circuit board.
A Step-By-Step Guide to PCB Drilling Process
The precise procedures for PCB board drilling may vary significantly from one manufacturer's tools and methods to another, but generally this involves the following steps:
Data Preparation:
Designers are responsible for preparing the necessary data, which includes the drill file that specifies the exact placement, size, and kind of holes required in the PCB design.Panel Preparation:
To prepare the PCB board fabrication panels, which consist of several PCBs arrayed on a single bigger sheet are cleaned and pre-drilled.
Drilling:
When drilling, a computer numerically controlled (CNC) machine uses specialized drill bits and the supplied data to make holes on the PCB board with a high degree of accuracy. Various drilling techniques, including mechanical drilling and laser drilling, can be used to meet specific needs and accommodate varying hole sizes.
Deburring:
To prepare surfaces for subsequent processing, deburring is performed during this PCB manufacturing process after drilling to eliminate burrs and debris that may have been left around the margins of the holes.
Inspection and Cleaning:
The drilled panels are checked thoroughly to make sure the holes are the right size and meet all the requirements. Repairs or replacement of the panel may be necessary if any holes do not comply.
Different Drilling Techniques
The outcome of the process in terms of hole size, quality, and total PCB cost is greatly affected by the drilling technique you use. In a nutshell, these are the two primary approaches:
Mechanical Drilling:
The mechanical drilling method has been around for a long time and uses drill bits that spin at high speeds to bore holes. If your designs are basic, it's a great budget option for bigger holes (usually more than 100 microns).
Laser Drilling:
For high-density printed circuit boards and intricate designs, laser drilling is an indispensable tool for making tiny, precisely sized holes (down to 10 microns) using a concentrated laser beam.
At PCB Power, we understand the intricacies involved in PCB fabrication, including the precision required in drilling. With our state-of-the-art equipment and skilled technicians, we ensure the high quality PCBs for your projects. Whether you're a hobbyist or a large-scale OEM, we an cater to all your EMs needs from providing PCB Layout to PCB assembly. Contact us today to learn more about our services and how we can help bring your electronic designs to life.