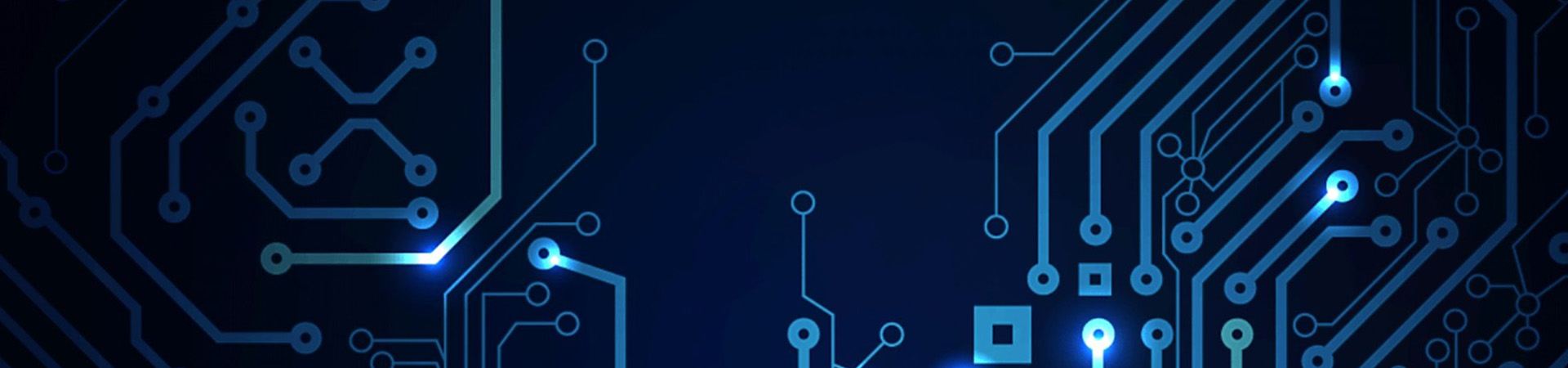
In the world of printed circuit boards (PCBs), every detail matters. One crucial factor that often goes unnoticed but can have a significant impact on the performance and reliability of electronic devices is PCB cavity. In this in-depth technical blog, we will explore what a PCB cavity is, why it occurs, its effects, and most importantly, how designers and engineers can prevent it.
What is PCB Cavity?
PCB cavity, also known as voiding or outgassing, refers to the presence of air pockets or gaps within the internal structure of a printed circuit board. These cavities can occur within the substrate material, between layers, or within solder joints. The formation of PCB cavities can compromise the structural integrity of the board and negatively affect its electrical and thermal performance.
Causes of PCB Cavity:
Resin Trapping: During the lamination process, air may get trapped between the layers of the PCB if not properly evacuated. This trapped air can create voids in the substrate.
Outgassing:
Some materials used in PCB manufacturing may release gasses when exposed to high temperatures, leading to the formation of voids. This is especially common in certain types of solder masks and PCB laminates.
Inadequate Soldering:
Insufficient solder paste or improper reflow soldering techniques can result in voids within solder joints, which can affect electrical connections.
Effects of PCB Cavity:
Understanding the potential consequences of PCB cavity is crucial for designers and engineers:
Electrical Performance:
Voids within copper traces or solder joints can increase electrical resistance, leading to signal degradation, voltage drops, and potential circuit failures.
Thermal Issues:
PCB cavities can hinder the dissipation of heat, causing localized hotspots and reducing the overall thermal efficiency of the board.
Mechanical Weakness:
The presence of voids can weaken the structural integrity of the PCB, making it more susceptible to physical damage, such as cracking or delamination.
Preventing PCB Cavity:
To ensure the reliability and performance of PCBs, it's essential to take preventive measures:
Proper Material Selection:
Choose PCB material with low outgassing properties and high-quality laminates that are less likely to trap air during lamination.
Optimized Lamination Process:
Implement proper vacuum and pressure controls during the lamination process to minimize the risk of air entrapment.
Soldering Techniques:
Use precise solder paste application techniques and ensure proper reflow soldering profiles to minimize voids in solder joints.
X-ray Inspection:
Employ X-ray inspection equipment to detect and locate voids within the PCB, allowing for timely corrections.
Design Considerations:
Design PCBs with adequate ground planes, thermal vias, and proper component placement to enhance heat dissipation and minimize the impact of voids.
Conclusion: PCB cavity is a subtle but significant issue in PCB manufacturing. Designers and engineers must be aware of its causes, effects, and preventive techniques to ensure the reliability and performance of electronic devices. By taking proactive measures in material selection, manufacturing processes, and design considerations, they can minimize the occurrence of PCB cavities and deliver high-quality, reliable circuit boards.