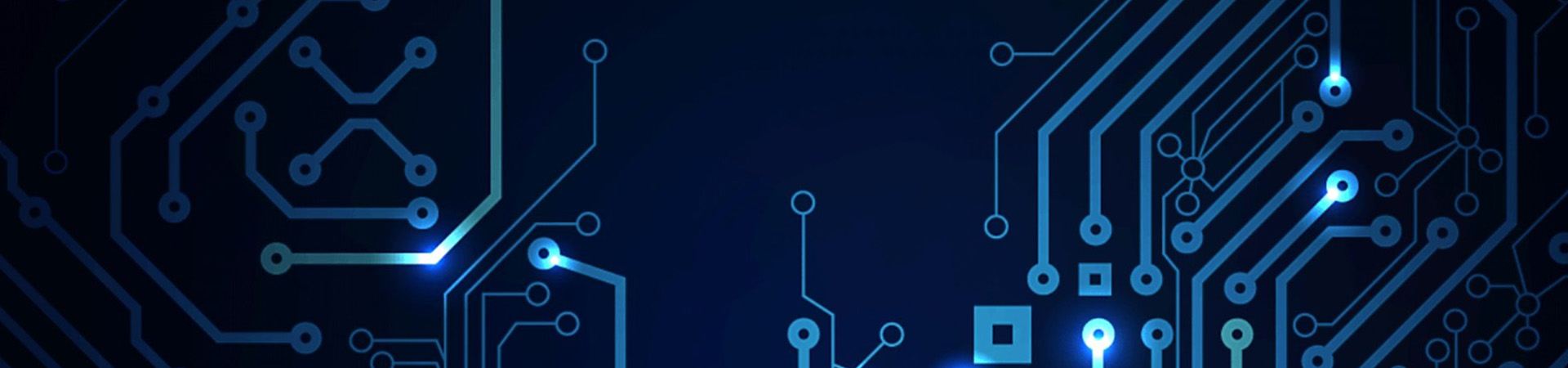
What are Flexible Printed Circuit Boards and their Advantages
Often, the nature of requirements of modern electronic equipment are contradictory. For instance, the products need to be light but capable of withstanding environments with heat and vibration. Moreover, to make the product at a low cost, it must be machine-assembled. Quality and reliability are necessary to withstand competition. As if all this was not enough, product life cycles demand rapid prototyping and implementation, as a low time to market is essential for establishing a product line. Flexible printed circuit boards are versatile enough to not only meet the above requirements but can also be used in a wide range of applications, from consumer electronics to aerospace and medical.
Over the past few decades, electronic devices have been shrinking in form factor. That means the printed circuit board inside must also be smaller. While it may not be possible to shrink the size of a regular rigid board, transferring the circuit to a flexible PCB has the advantage of making better use of the limited space inside the device. In fact, flexible PCBs offer the designer significant amounts of freedom, allowing them to make lightweight and durable products.
What are Flexible PCBs?
As is evident from the name, flexible PCBs are made of thin substrates, which are flexible enough to bend repeatedly. Along with high physical flexibility, these innovative boards also have good tensile strength. Being flexible, the designer can mold flexible PCBs into complex shapes to fit three-dimensional spaces. This feature allows the use of flexible boards in diverse applications like medical care, modern hearing aids, several minuscule devices, wearable technology, and aerospace piloting.
Although the thickness of a flex PCB may be only a few microns, fabricators can etch it reliably. This makes flexible PCBs more suitable for some applications as compared to rigid PCBs. For instance, replacing traditional wire harnesses and ribbon connectors with flexible PCBs renders the system with high reliability and durability.
It is possible to form flex circuits in complex shapes in three dimensions along with branches to multiple connectors. This would be impossible to achieve with a ribbon cable. Moreover, it is possible to interface flex circuits with rigid boards without any bulky connectors that flat cables usually require. In the case of rigid-flex construction, the flexible part can be an integral part of rigid boards, thereby eliminating all external connectors. Furthermore, the conductor density of flex circuits can be much higher than that of ribbon cables.
Classes of Flexible PCBs
Depending on the performance requirements of the finished product, level of inspection, and testing, there are three different classes of flexible circuits:
Class I Flexible PCBs
Class I flexible circuits are suitable for general electronic products like consumer electronics, computer peripherals, and some computer applications. These products require bare minimum inspection, testing, and low performance standards. Disposable electronic products use Class I flexible PCBs.
Class II Flexible PCBs
Class II flexible PCBs are suitable in electronic products for dedicated purposes. Examples of such products are sophisticated business machines, communication equipment, instruments requiring extended life and high performance, and those for which uninterrupted service is a desired feature but not a critical one.
Such printed circuit boards require medium inspection, testing, and performance standards. This makes them more expensive than the Class I types. Medical diagnostic equipment, smartphones, and cameras are some products that use Class II flexible PCBs.
Class III Flexible PCBs
Class III type of flexible circuits are suitable for high-reliability electronics. This includes products and equipment that must perform continuously on-demand in critical conditions and equipment for which downtime cannot be tolerated and must function when required. Examples of such equipment are flight control systems and life support items.
Class III flexible PCBs are suitable for applications demanding high levels of assurance and service. They require the highest levels of inspection, testing, and must meet a high degree of performance standards. Among the three classes, Class III printed circuit board prices are the highest. Mostly military/aerospace electronics and medical devices for life support use Class III flexible PCBs.
Types of Flexible PCBs
Depending on the number of layers, type of construction, the materials used, and the presence or absence of plated-through holes, flexible printed circuit boards can be graded into five types:
IPC Type I Flexible PCB
These are single-sided flexible boards. Ideal for dynamic flex applications, these are the most common types available. As there is only one conductive layer, SMT lands are accessible from one side only. IPC Type I flex PCBs do not have any plated through holes, and it is possible to use them with or without stiffeners.
IPC Type II Flexible PCBs
These are double-sided flexible boards. They have two conductor layers and are plated through holes. It is possible to use them with or without stiffeners. Circuit board fabrication is similar to regular PCBs, with copper film bonded on both sides of the base material. This combination then undergoes drilling, plating, etching, and insulation on both sides with a dielectric coverlayer.
IPC Type III Flexible PCBs
These are multilayer flexible boardsmultilayer flexible boards. They can contain three or more conductive layers along with plated through holes for creating interconnections between the conductive layers. It is possible to use them with or without stiffeners.
IPC Type IV Flexible PCBs
These are multi-layered flexible boards in combination with rigid parts. They can have three or more conductive layers along with plated through holes.
IPC Type V Flexible PCBs
These are flexible or a combination of rigid and flexible circuit boards. They may have two or more conductive layers but no plating through holes.
Advantages of Flexible PCBs
Unlike rigid boards, flexible printed circuit boards unlock various physical design advantages such as:
- Capability of bending 360 degrees
- Superior resistance to vibrations
- Capability of withstanding higher temperatures
- Ability to withstand several types of disruptions in harsh environments
- Ability to support compact and lightweight design
- Ability to significantly reduce product weight
- Can replace wire harnesses with small and flexible cables, taking up less space
- Ability to warp or contort without any associated damage.
Flexible circuits offer significant manufacturing advantages also:
- They permit better airflow
- They allow better heat dissipation
- The number of interconnections is lower
- Lower susceptibility to assembly errors
Conclusion
Flexible printed circuit boards are eminently suitable for connecting internal systems of complex modern electronic devices. Being more versatile and flexible, these are the preferred circuits for use in aerospace, medical, and consumer technology. With flexible printed circuit boards, designers can make thinner, and more compact products.